Leveraging the 5 WHYs Principle for Seamless Transitions
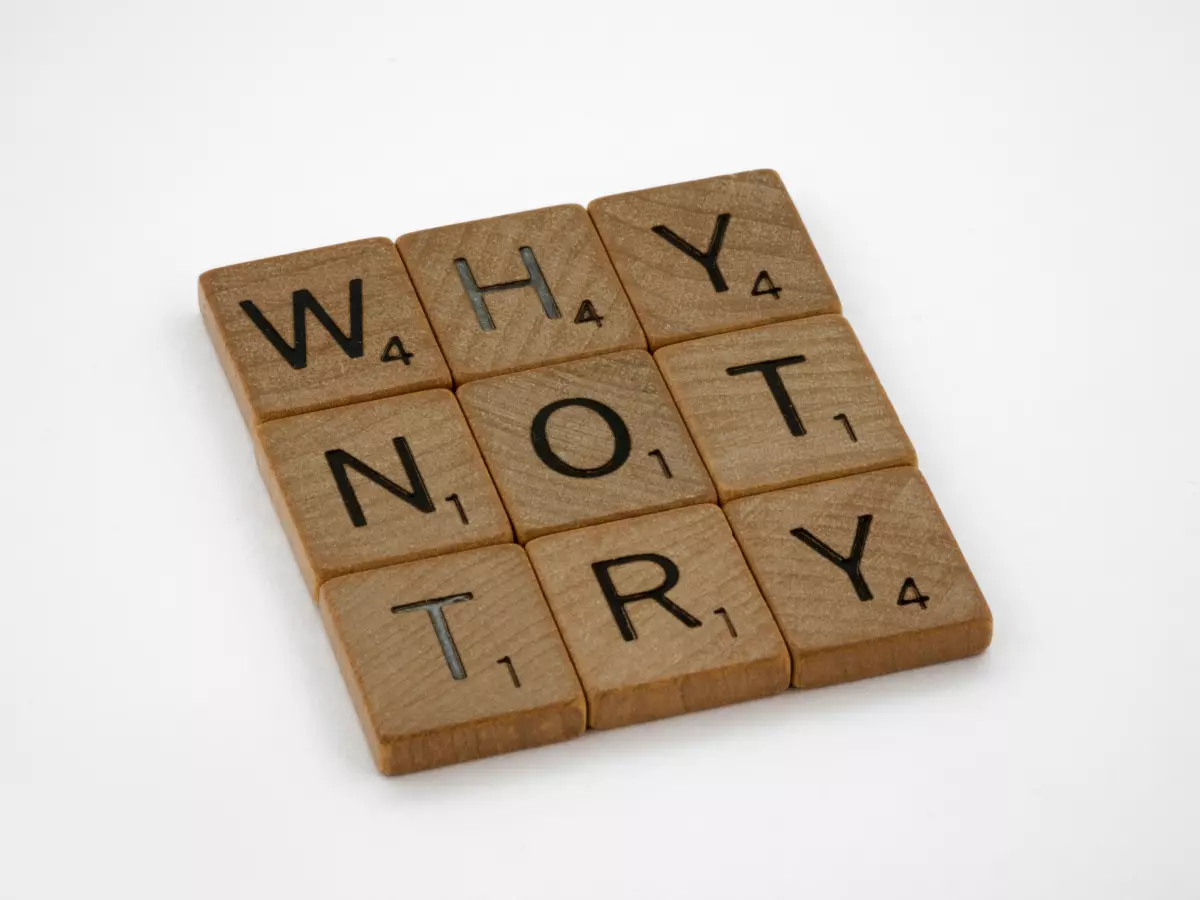
In the dynamic world of project management, the cutover phase is a critical juncture that can make or break a project’s success. This phase, marking the transition from old systems to new, demands meticulous planning and execution to minimize disruptions and ensure seamless integration.
One powerful tool that can significantly enhance this process is the 5 WHYs principle.
Developed by Sakichi Toyoda for the Toyota Production System, the 5 WHYs is a root cause analysis technique that helps identify underlying issues by asking “Why?” iteratively.
In this comprehensive article, we will explore how to effectively use the 5 WHYs principle in cutover management to drive success and continuous improvement.
Understanding the 5 WHYs Principle
The 5 WHYs principle is a straightforward yet powerful technique for uncovering the root causes of problems. Here’s a breakdown of its core components:
Origin and Concept:
Developed by Sakichi Toyoda, the founder of Toyota Industries, the 5 WHYs technique was later popularized by Taiichi Ohno, the architect of the Toyota Production System.
The method involves asking “Why?” five times to get to the heart of a problem, although the number five is not a strict rule but rather a guideline.
Importance in Problem-Solving:
The 5 WHYs shifts the focus from addressing symptoms to tackling the underlying causes, ensuring that issues are resolved at their core.
This approach is particularly valuable in cutover management, where understanding and mitigating root causes can prevent recurring issues and enhance the overall transition process.
The Role of the 5 WHYs in Cutover Management
Cutover management involves a series of carefully orchestrated steps to transition from an old system to a new one. Here’s how the 5 WHYs can be integrated into this process:
Defining the Problem:
Clearly articulate the issues encountered during the cutover.
For example, “The data migration process is taking longer than expected.“
Precise problem definition ensures that the 5 WHYs analysis starts on the right foot.
Asking “Why?” Iteratively:
1st Why: Why is the data migration process taking longer than expected?
Answer: Because the data validation step is more complex than anticipated.
2nd Why: Why is the data validation step more complex?
Answer: Because the data structures between the old and new systems are significantly different.
3rd Why: Why are the data structures different?
Answer: Because the new system has enhanced data integrity requirements.
4th Why: Why weren’t these differences addressed earlier?
Answer: Because the initial data mapping process was rushed.
5th Why: Why was the data mapping process rushed?
Answer: Because the project timeline did not allocate sufficient time for thorough data mapping.
Identifying the Root Cause:
In this example, the root cause is the insufficient time allocated for thorough data mapping. Addressing this root cause involves adjusting the project timeline and ensuring adequate resources are allocated for comprehensive data mapping.
Implementing the 5 WHYs in Cutover Planning
To effectively use the 5 WHYs in cutover planning, follow these steps:
Pre-Cutover Preparation:
Integrate the 5 WHYs into the dress rehearsal phase to anticipate and mitigate potential risks.
Conduct a thorough review using the 5 WHYs to identify lessons learned and develop action plans based on the insights gained.
Post-Dress Rehearsal Analysis:
After the dress rehearsal, gather your team to reflect on what went wrong and what can be improved.
Use the 5 WHYs to drive your Lessons Learned Session, ensuring that you uncover detailed insights into the issues encountered.
Enhancing the Cutover Strategy:
Refine your cutover plan to address the identified root causes.
Ensure alignment with the overall project goals and timelines.
Best Practices for Effective Use of the 5 WHYs
To maximize the effectiveness of the 5 WHYs in cutover management, consider the following best practices:
Involving the Right Stakeholders:
Include diverse perspectives in the analysis to ensure a comprehensive understanding of the issues.
Facilitate productive 5 WHYs sessions by encouraging open discussion and probing questions.
Documenting Findings:
Create a comprehensive record of the 5 WHYs process and outcomes.
Share insights with the project team and stakeholders to foster transparency and collaboration.
Continuous Improvement:
Incorporate the 5 WHYs into regular project reviews and retrospectives.
Foster a culture of continuous learning and improvement by regularly applying the 5 WHYs to identify and address root causes.
Stopping at Symptoms:
Ensure that the analysis goes deep enough to uncover the true root cause.
Avoid settling for superficial answers by pushing beyond the first plausible explanation.
Lack of Data or Evidence:
Base your answers on facts and observable evidence rather than assumptions.
Involve team members who have firsthand knowledge of the issue to ensure accurate insights.
Blame Game:
Focus on improving processes rather than assigning blame.
Encourage a psychologically safe environment where team members feel comfortable sharing honestly.
Integrating the 5 WHYs into Your Project Management Workflow
To seamlessly incorporate the 5 WHYs into your project management workflow, consider the following strategies:
Make it a Regular Practice:
Schedule regular 5 WHYs sessions as part of your project management routine.
Incorporate the 5 WHYs into retrospectives and use it to analyze patterns in customer feedback or support tickets.
Create a Culture of Curiosity:
Lead by example and demonstrate the value of asking “Why?” in meetings and discussions.
Encourage questioning and reward root cause identification to foster a culture of continuous improvement.
Integrate with Other Tools and Processes:
Combine the 5 WHYs with data analysis to focus on the most relevant metrics.
Use the 5 WHYs in user research and feature prioritization to ensure that you’re addressing root needs rather than surface-level wants.
Conclusion
The 5 WHYs principle is a powerful tool for identifying and addressing root causes in cutover management.
By integrating this technique into your cutover planning and execution, you can enhance the success of your transitions, minimize risks, and foster a culture of continuous improvement.
Embrace the 5 WHYs to drive meaningful improvements and ensure a smooth and successful cutover process.